 |
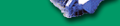







 
|
 |
|
Participant ABB Environmental
Systems
Location Niles, Trumbull County,
OH (Ohio Edison's Niles Station, Unit No. 2)
Plant Capacity/Production 35-MWe
equivalent slipstream from a 108-MWe boiler
Coal Ohio bituminous, 3.4%
sulfur
Technology Haldor Topsoe's SNOX™
catalytic advanced flue gas cleanup system |
|
Additional Team Members Ohio Coal
Development Office cofunder Ohio Edison
Company cofunder and host Haldor Topsoe
a/s patent owner for process technology, catalysts, and WSA
tower Snamprogetti, U.S.A. cofunder and process
designer |
|
Project Funding |
Total cost DOE Participant |
$31,438,408 $15,719,200 $15,719,208 |
100% 50% 50% | |
|
SNOX is a trademark of Haldor Topsoe a/s.
|
Project Objective
To demonstrate at an electric power plant using U. S. high-sulfur coals
that SNOX™ technology will catalytically remove 95% of SO2 and
more than 90% of NOx from flue gas and produce a salable
by-product of concentrated sulfuric acid.
In the SNOX™ process, the stack gas leaving the boiler is cleaned of
fly ash in a high-efficiency fabric filter baghouse to minimize the
cleaning frequency of the sulfuric acid catalyst in the downstream
SO2 converter. The ash-free gas is reheated , and
NOx is reacted with small quantities of ammonia in the first of
two catalytic reactors where the NOx is converted to harmless
nitrogen and water vapor. The SO2 is oxidized to SO3
in a second catalytic converter. The gas then passes through a novel
glass-tube condenser that allows SO3 to hydrolyze to
concentrated sulfuric acid.
The technology, while using U.S. coals, was designed to remove 95% of
the SO2 and more than 90% of the NOx from flue gas
and produce a salable sulfuric acid by-product. This was accomplished
without using sorbents and without creating waste streams.
The demonstration was conducted at Ohio Edison's Niles Station in
Niles, OH. The demonstration unit treated a 35-MWe equivalent slipstream
of flue gas from the 108-MWe Unit No. 2 boiler, which burned a 3.4% sulfur
Ohio coal. The process steps were virtually the same as for a commercial
full-scale plant, and commercial-scale components were installed and
operated.
|
SNOXTM Flue Gas
Cleaning Demonstration Project Process Flow Diagram Larger jpeg or wmf version |
Environmental
-
SO2 removal efficiency was normally in excess of 95% for
inlet concentrations averaging about 2,000 ppm.
-
NOx reduction averaged 94% for inlet concentrations of
approximately 500-700 ppm.
-
Particulate removal efficiency for the high-efficiency fabric filter
baghouse with SNOX™ system was greater than 99%.
-
Sulfuric acid purity exceeded federal specifications for Class I
acid.
-
Air toxics testing showed high capture efficiency of most trace
elements in the baghouse. A significant portion of the boron and almost
all of the mercury escaped to the stack. But selenium and cadmium,
normally a problem, were effectively captured in the acid drain, as were
organic compounds.
-
Absence of an alkali reagent contributed to having no secondary
pollution streams or increases in CO2 emissions.
-
Presence of the SO2 catalyst virtually eliminated CO and
hydrocarbon emissions.
Operational
-
Having the SO2 catalyst downstream of the NOx
catalyst eliminated ammonia slip and allowed the SCR to function more
efficiently.
-
Heat developed in the SNOX™ process was used to enhance thermal
efficiency.
Economic
Because the SNOX™ process utilized an oxidation catalyst to convert
SO2 to SO3 and ultimately to sulfuric acid, no
reagent was required for the SO2 removal step. As a result, the
process produced no other waste streams.
In order to demonstrate and evaluate the performance of the SNOX™
process, general operating data were collected and parametric tests
conducted to characterize the process and equipment. The system has
operated for approximately 8,000 hours and produced more than 5,600 tons
of commercial-grade sulfuric acid. Many tests for the SNOX™ system were
conducted at three loads—75%, 100%, and 110% of design capacity.
Environmental Performance
Particulate emissions from the process were very low (< 1
mg/Nm3) due to the characteristics of the SO2
catalyst and the sulfuric acid condenser (WSA Condenser). The Niles SNOX™
plant was fitted with a baghouse (rather than an ESP) on its inlet.
This was not necessary for low particulate emissions, but rather was
needed to maintain an acceptable cleaning frequency of the SO2
catalyst. At operating temperature, the SO2 catalyst, because
of its sticky surface, retained about 90% of the dust that entered the
catalyst vessel. Dust that passed through was subsequently removed in the
WSA Condenser, which acted as a condensing particulate removal device
(utilizing the dust particulates as nuclei).
Minimal or no increase in CO2 emissions by the process was
tied to two features--the lack of a carbonate-based alkali reagent that
releases CO2 and the fact that the process recovered additional
heat from the flue gas to offset its parasitic energy requirements. This
heat recovery, under most design conditions, results in the net heat rate
of the boiler being the same or better after addition of the SNOX™
process, and consequently no increase in CO2 generation per
unit of power.
With respect to CO and hydrocarbons, the SO2 catalyst acted
to virtually eliminate these compounds as well. This aspect also
positively affected the interaction of the NOx and
SO2 catalysts. Because the SO2 catalyst followed the
NOx catalyst, any unreacted ammonia (slip) was oxidized in the
SO2 catalyst to nitrogen, water vapor, and a small amount of
NOx . As a result, downstream fouling by ammonia compounds was
eliminated and the SCR was operated at slightly higher than typical
ammonia stoichiometries. These higher stoichiometries allowed smaller SCR
catalyst volumes and permitted the attainment of very high reduction
efficiencies (>95%).
Sulfur dioxide removal in the SNOX™ process was controlled by the
efficiency of the SO2-to-SO3 oxidation, which
occurred as the flue gas passes through the oxidation catalyst beds. The
efficiency was controlled by two factors--space velocity and bed
temperature. Space velocity governed the amount of catalyst necessary at
design flue gas flow conditions, and gas and bed temperature had to be
high enough to activate the SO2 oxidation, reaction. During the
test program, SO2 removal efficiency was normally in excess of
95% for inlet concentrations averaging about 2,000 ppm.
|
The bottom portion of the
SO2 converter catalyst, with the catalyst dust collector
hopper mounted on steel rails (center), is shown. |
The SCR portion of the SNOX™ process was able to operate at higher than
typical ammonia stoichiometries due to its location ahead of the
SO2 catalyst beds. Normal operating stoichiometries for the SCR
system were in the range of 1.02-1.05 and system reduction efficiencies
averaged 94% with inlet NOx levels of approximately 500-700
ppm.
Sulfuric acid concentration and composition has met or exceeded the
requirements of the federal specifications for Class I acid. During the
design and construction of the SNOX™ demonstration, arrangements were made
with a sulfuric acid supplier to purchase and distribute the acid from the
plant. The acid has been sold to the agriculture industry for the
production of diammonium phosphate fertilizer and to the steel industry
for pickling. Ohio Edison has also used a significant amount in boiler
water demineralizer systems throughout its plants.
Air toxic testing conducted at the Niles SNOX™ plant measured the
following substances:
-
Five major and 16 trace elements including mercury, chromium,
cadmium, lead, selenium, arsenic, beryllium, and nickel
-
Acids and corresponding anions (hydrogen chloride, hydrogen fluoride,
chloride, fluoride, phosphate, sulfate)
-
Ammonia and cyanide
-
Elemental carbon
-
Radionuclides
-
Volatile organic compounds
-
Semi-volatile compounds including polynuclear aromatic hydrocarbons
-
Aldehydes
Most trace elements were captured in the baghouse along with the
particulate. A significant portion of the boron and almost all of the
mercury escaped to the stack. But selenium and cadmium, normally a
problem, were effectively captured in the acid drain, as were organic
compounds.
Operational Performance
Heat recovery was accomplished by the SNOX™ process. In a commercial
configuration, it can be utilized in the thermal cycle of the boiler. The
process generated recoverable heat in several ways. All of the reactions
that took place with respect to NOx and SO2 removal
were exothermic and increased the temperature of the flue gas. This heat
plus fuel-fired support heat added in the high-temperature
SCR/SO2 catalyst loop was recovered in the WSA Condenser
cooling air discharge for use in the furnace as combustion air. Because
the WSA Condenser lowered the temperature of the flue gas to about 210° F,
compared to approximately 300° F for a typical power plant, additional
thermal energy was recovered along with that from the heats of reaction.
Economic Performance
The economic evaluation of the SNOX™ process showed a capital cost of
approximately $305/kW for a 500-MWe unit firing 3.2% sulfur coal. The
levelized incremental cost was 6.1 mills/kWh on a constant dollar basis
and 7.8 mills/kWh on a current dollar basis. The equivalent costs per ton
of SO2 removed were $219/ton (constant dollars) and $384
(current dollars).
|
The SNOX™
demonstration at Ohio Edison's Niles Station Unit No. 2 achieved
SO2 removal efficiencies exceeding 95% and NOx
reduction effectiveness averaging 94%. Ohio Edison is retaining the
SNOX™ technology as part of its environmental control system.
|
The SNOX™ technology is applicable to all electric power plants and
industrial/institutional boilers firing coal, oil, or gas. The high
removal efficiency for NOx and SO2 makes the process
attractive in many applications. Elimination of additional solid waste
(except ash) enhances the marketability in urban and other areas where
solid waste disposal is a significant problem.
The host utility, Ohio Edison, is retaining the SNOX™ technology as a
permanent part of the pollution control system at Niles Station to help
Ohio Edison meet its overall SO2/NOx reduction
goals.
Commercial SNOX™ plants also are operating in Denmark and Sicily. In
Denmark, a 305-MWe plant has operated since August 1991. The boiler at
this plant burns coals from various suppliers around the world, including
the United States; the coals contain 0.5-3.0% sulfur. The plant in Sicily,
operating since March 1991, has a capacity of about 30 MWe and fires
petroleum coke.
Paul Yosick, Project Manager ABB Environmental Systems 1409
Center Port Boulevard Knoxville, TN 37932 (423) 693-7550 (423)
694-5213 (fax) paul.yosick@usapc.mail.abb.com
Lawrence Saroff, DOE/HQ, (301) 903-9483 lawrence.saroff@hq.doe.gov
James U. Watts, NETL, (412) 386-5991 mailto:watts@fetc.doe.gov |
 |